The Old Foundry: Lessons Learnt From The Conversion Of A Victorian Building
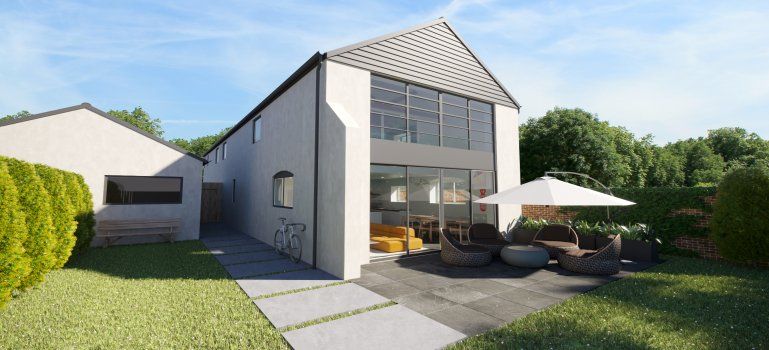
No matter how carefully you plan, life is always taking you by surprise. On a construction site it’s the same, like what happened on our Old Foundry project site. Unexpected findings can break your day and the only way to win is to find the bright side of things!
So if life gives you a steel beam in the middle of a staircase opening, well, don’t make lemonade!
Note: now that the project is complete, you can have a look at the final result here.
A Beam Is Found Where The Architects Designed A Staircase Opening: A Cost And Time Effective Solution
While creating the opening for a staircase, we found an existing steel beam not shown in the drawings as it wasn’t visible before the stripping out.
A decision was made on-site after the real time assessment of our structural engineer. He foun d it was safe to remove the beam and place it in a different position coherent with the rest of the design, without compromising the stability both during the alteration and in the final result.
By having a structural engineer on site we can skip the standard procedure of interrupting the work, contacting the architects, arranging a site visit with the original structural engineers and wait for them to produce a new design.
Our client saved time and avoided the additional cost of the involvement of the architect and the original structural engineer.
The Joists Run In The Opposte Direction That The Architect Assumed In Their Drawings
When creating an opening for a staircase, we found that the direction of the joists assumed on the drawings was wrong. This is not uncommon as the joists are not usually exposed during the design phase.
One of the solutions could be to cut some of the joists and add an extra steel beam to support them. In this particular case, this wouldn’t be ideal, because the beam would be visible inside an adjacent extension with sloped roof and even outside of the sloped roof itself. Alternatively, a column would be needed in the middle of an open space.
In a standard situation, the original structural engineers would need to inspect and provide new drawings according to the newly found situation. In our case our engineer assessed the situation on-site and managed to create a brilliant alternative: using an existing internal wall to bear the load of the cut timber floor joists, we solved the problem with a small alteration to the original wall to make it load bearing, that is, by building it with concrete blocks.
We avoided delays and the additional cost of a steel element, plus we implemented a solution that did not deteriorate the habitability and aesthetics of the room.
Structural Frames And Other Solutions When Replacing A Wall With Glazing
The initial design included the creation of a wide opening at the back of the building that required a steel frame to provide additional support. The structural elements were two horizontal beams and two additional columns positioned at the sides of the opening and supported by new pad foundations.
After exposing the walls and inspecting the foundations, we realised the additional foundations and columns were not required. We applied structural design optimisation, bolting the horizontal beams to the lateral walls. That way we achieved the right vertical load distribution and we also increased the horizontal stability by connecting the two walls.
Through our optimisation, our client saved money and reduced the amount of work required.
Regular Inspections Of Existing Structural Elements, Included Brick Walls, Prevent Future Costly Problems
During a site inspection we realised the external brick-walls were in poor condition. We decided to strengthen the existing walls and stop the deterioration of the bricks by using rich mix sand and cement render on the external face of the walls. This method enhances the performance of brick masonry walls, increases their shear strength and the overall structure’s performance. Without a structural engineer on-site, that might go unnoticed by the builder and eventually compromise the quality of the final result; in alternative, a structural engineer would need to visit the site to create a conditional report with remedial recommendations.
Vinz is the CEO and co-founder of houseUP. He is a true authority in financial planning and risk management, coming from years of working in financial services and digital payment industries
houseUP is a construction company in London, specialised in high end residential and commercial projects.